The Ultimate Guide to Lubrication Fittings for Your Business
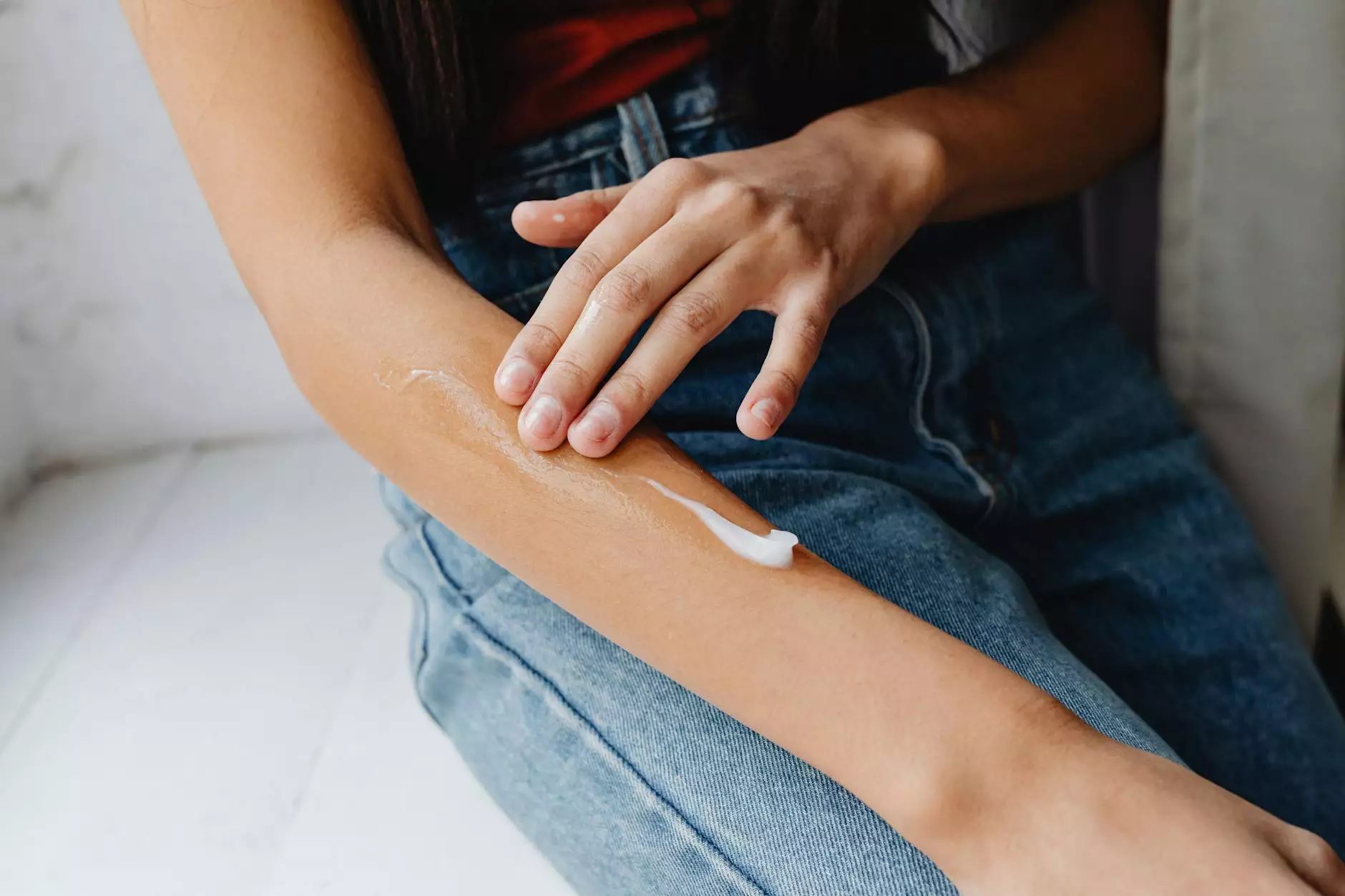
In the fast-paced world of industry and manufacturing, the importance of maintaining machinery cannot be overstated. One critical component that ensures machinery operates smoothly is lubrication fittings. These small devices play a vital role in the efficiency, longevity, and maintenance of equipment across multiple sectors. In this comprehensive guide, we will explore everything you need to know about lubrication fittings, including their types, benefits, and best practices for use.
What Are Lubrication Fittings?
Lubrication fittings, often referred to as grease fittings or zerk fittings, are small mechanical devices that allow for the easy injection of lubricant into moving parts of machinery. They serve as portals for grease, oils, or other lubricants to reduce friction between components, preventing wear and tear that can lead to breakdowns and costly repairs.
Types of Lubrication Fittings
Understanding the various types of lubrication fittings is crucial for selecting the right one for your equipment. Here are the most common types:
- Zerk Fittings: The most common type, these fittings feature a one-way valve that allows grease to enter while preventing it from escaping. They are typically used on ball joints, wheel bearings, and other pivot points.
- Friction Fittings: Designed to fit tightly into the component, these fittings are not commonly used but can be effective in applications requiring constant lubrication without regular servicing.
- Parker Fittings: A brand known for its reliability, Parker fittings often come in a variety of styles, providing robust solutions for various machinery applications.
- Screw Fittings: These fittings require a specific tool for installation. They are generally utilized in systems where space is limited.
- Push-to-Connect Fittings: Designed for easy installation, these fittings allow for rapid connection and disconnection without the use of tools.
Benefits of Using Lubrication Fittings
The integration of lubrication fittings within your machinery can yield numerous benefits, including:
- Enhanced Lifespan of Equipment: Regularly lubricated equipment experiences less wear and tear, significantly extending its operational life.
- Improved Efficiency: Lubricated components operate smoother, reducing energy consumption and increasing overall efficiency.
- Reduced Downtime: Effective lubrication minimizes the risk of breakdowns, leading to less unplanned downtime and higher productivity.
- Cost-Effective Maintenance: Incorporating lubrication fittings simplifies maintenance routines, allowing for quicker and more efficient service.
How to Choose the Right Lubrication Fittings
Selecting the appropriate lubrication fitting for your machinery is critical. Here are the steps to consider:
- Identify Your Machinery's Needs: Understand the type of machinery and its lubrication requirements—consult manufacturer guidelines if needed.
- Evaluate Operating Conditions: Consider the environment in which the machinery operates. Harsh conditions may require robust fittings designed to withstand external factors.
- Choose the Right Material: Lubrication fittings come in various materials, including brass, steel, and plastic. Choose a material compatible with your lubricant and environment.
- Consult an Expert: If unsure, consulting with a lubrication expert or the manufacturer can provide significant insights.
Maintenance Tips for Lubrication Fittings
To ensure the longevity and effectiveness of lubrication fittings, implementing regular maintenance is essential. Follow these tips:
- Regular Inspections: Check fittings for wear and damage routinely. Look for any signs of leakage or blockage.
- Proper Lubrication: Use the correct type of lubricant as specified for your machinery. Over or under lubrication can cause issues.
- Cleaning: Regularly clean fittings to prevent debris build-up, which can obstruct lubricant flow.
- Replacement: Replace any damaged fittings immediately to avoid further complications.
Common Applications of Lubrication Fittings
Lubrication fittings find applications in numerous industries and machinery, including:
- Agriculture: Tractors and combines require proper lubrication to function efficiently in the field.
- Manufacturing: Conveyor belts and bearings in production facilities rely on consistent lubrication to maintain operation.
- Aerospace: Precision machinery in aviation demands exceptional care in lubrication to ensure safety and performance.
- Automotive: Vehicles utilize lubrication fittings in various components, from wheel bearings to engine parts.
- Construction: Heavy machinery such as excavators and bulldozers depend heavily on regular lubrication for optimal performance.
Innovative Technologies in Lubrication Fittings
As technology evolves, so does the design and functionality of lubrication fittings. Innovation has led to developments such as:
- Automatic Lubrication Systems: These systems provide consistent, timed lubricant delivery, mitigating the risk of human error.
- Smart Lubrication Monitoring: Sensors and IoT technology allow operators to monitor lubricant levels and conditions in real-time, ensuring optimal performance.
- Environmentally Friendly Lubricants: The shift towards biodegradable lubricants demands fittings designed to accommodate new materials and specifications.
Where to Buy Lubrication Fittings
If you're in the market for high-quality lubrication fittings, consider purchasing from a reputable supplier. One such business that offers a range of fittings for sale is fitsch.cn. Their inventory is designed to meet the diverse needs of various industries while ensuring quality and reliability.
Conclusion
In conclusion, lubrication fittings are essential components that contribute significantly to the efficiency and durability of machinery. By understanding their types, benefits, and maintenance strategies, businesses can enhance their overall operational performance. Whether you're involved in agriculture, manufacturing, or any industry relying on machinery, incorporating and properly maintaining lubrication fittings should be a top priority for maintaining your equipment.
Investing time to learn about the correct use of lubrication fittings can lead to substantial long-term savings, improved productivity, and a more efficient operational framework. Always stay updated with the latest innovations in lubrication technology to ensure your machinery is equipped with the best solutions available.