The Essential Role of a Plastic Tooling Manufacturer in the Modern Economy
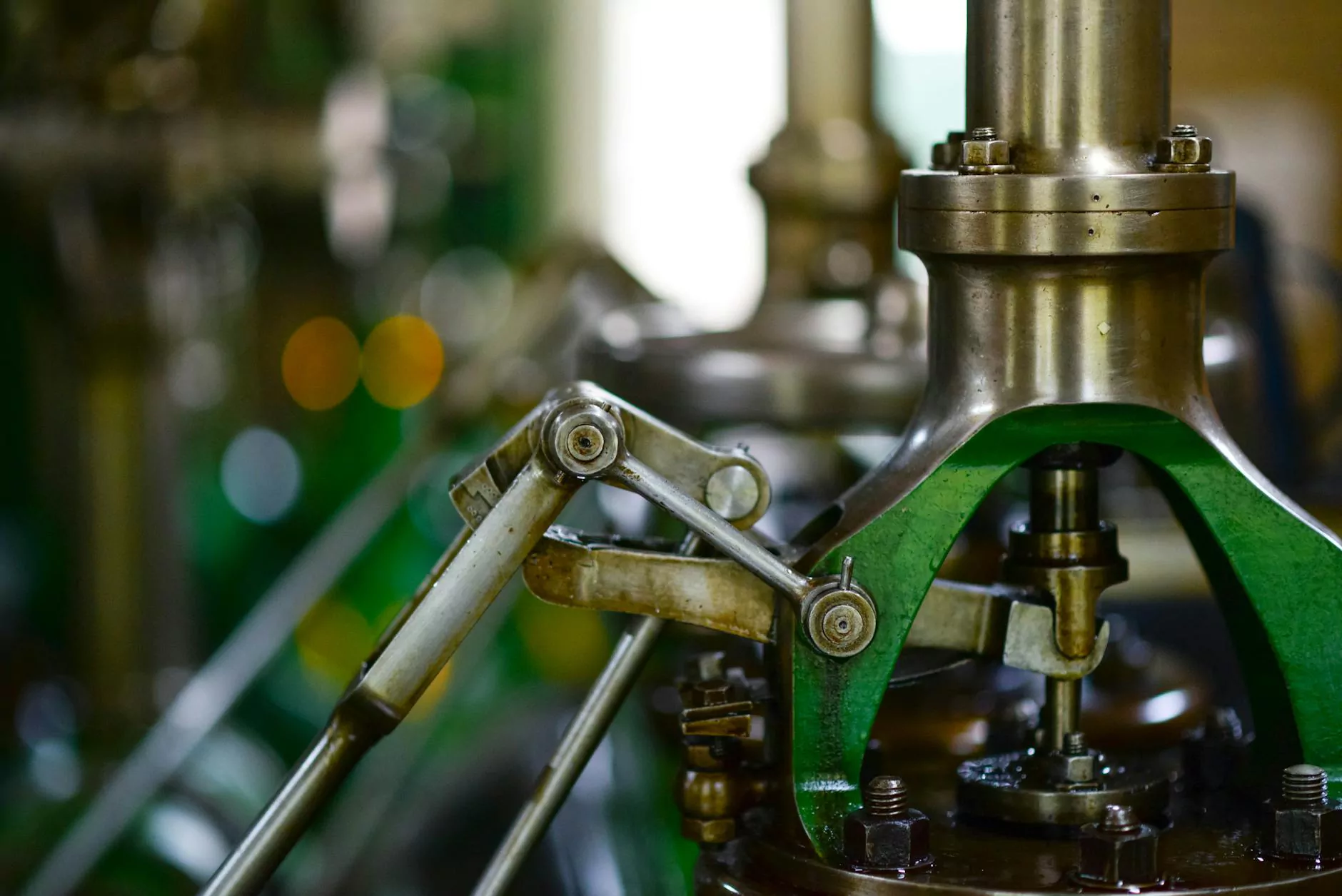
In today’s highly competitive manufacturing environment, the role of a plastic tooling manufacturer is paramount. These manufacturers are not just providers of tools; they are innovators and partners in the production process. Through advanced techniques and a thorough understanding of the materials they work with, they ensure that the manufacturing industry remains efficient and effective.
What is Plastic Tooling?
Plastic tooling refers to the techniques and tools used to create precise molds for manufacturing plastic products. The process typically involves the design, creation, and implementation of molds that will shape raw plastic into finished goods. Molds can be made using various materials depending on the product requirements, including aluminum, steel, and resin.
Importance of Plastic Tooling in Manufacturing
The significance of plastic tooling cannot be overstated. It serves several key functions in a variety of industries, including automotive, consumer goods, electronics, and healthcare. Here are some critical reasons why plastic tooling is vital:
- Precision and Accuracy: Plastic tooling ensures that products are produced with high precision, reducing waste and minimizing defects.
- Cost-Effective Production: By streamlining the manufacturing process, plastic tooling helps businesses save on production costs.
- Speed to Market: Efficient tooling processes enable faster turnaround times, allowing companies to respond quickly to market demand.
- Customization: Tooling can be tailored to meet specific product requirements, accommodating a wide range of designs and functions.
- Durability: High-quality tools result in longer-lasting production capabilities, which is essential for maintaining efficiency over time.
The Process of Plastic Tooling Manufacturing
The journey of creating effective plastic products starts with the design of the tooling. Here’s a breakdown of the critical steps involved:
1. Design Phase
The initial step involves creating a detailed design of the desired part or product. This often includes creating 3D models and simulations to visualize the end product. Collaboration between designers and engineers is essential here to ensure that all specifications are met.
2. Material Selection
A variety of materials can be used for tooling, including:
- Steel: Best for high-volume production due to its durability.
- Aluminum: Ideal for lower volume runs and quicker turnaround.
- Resin: Useful for prototype tooling and initial design stages.
3. Manufacturing the Tool
This phase involves machining, such as CNC milling, to create the physical tool based on the design specifications. Precision in this step is critical to ensure that the molds will perform correctly under production conditions.
4. Testing and Refinement
Once the tooling is complete, it undergoes rigorous testing to check for any defects or shortcomings. Adjustments and refinements are often necessary to perfect the tool’s performance.
5. Production Launch
After testing, the tool is ready for production. Designed to be robust and versatile, it can accommodate batch production of plastic parts efficiently.
Advantages of Collaborating with a Plastic Tooling Manufacturer
Choosing the right plastic tooling manufacturer can greatly influence a company’s production outcomes. Here are the benefits of making such a partnership:
- Expertise and Experience: Established manufacturers bring years of expertise that can be invaluable in navigating complex projects.
- Access to Advanced Technology: Many manufacturers invest in the latest technologies and processes, enabling more efficient production.
- Quality Assurance: A reputable manufacturer prioritizes quality and compliance with industry standards, ensuring reliability in production.
- After-Sales Support: Ongoing support in maintaining and optimizing tooling can greatly enhance productivity over time.
- Market Insights: Manufacturers often have insights into market trends and can help you adapt your products accordingly.
Case Study: Successful Plastic Tooling Applications
Consider the automotive industry, where precision and efficiency are paramount. A successful plastic tooling manufacturer was able to collaborate with a prominent car manufacturer to design and produce a series of lightweight components. By utilizing advanced material science and optimized tooling processes, they reduced production costs by 30% while shaving weeks off the manufacturing timeline.
Future Trends in Plastic Tooling Manufacturing
The landscape of plastic tooling is continuously evolving. Some emerging trends include:
- Additive Manufacturing: The rise of 3D printing technology is changing how tools are designed and produced, allowing for rapid prototyping and lower upfront costs.
- Smart Manufacturing: Integration of IoT (Internet of Things) and AI (Artificial Intelligence) for improved monitoring and optimization of production lines.
- Eco-Friendly Materials: A growing emphasis on sustainability is prompting manufacturers to explore biodegradable and recycled materials for both products and tooling.
- Customization and Automation: Increased demand for custom parts is leading to automation in tooling processes to maintain efficiency.
Conclusion
The role of a plastic tooling manufacturer is crucial in driving innovation and efficiency in the manufacturing industry. As businesses continue to seek higher precision, lower costs, and faster production times, the expertise of these manufacturers will become increasingly valuable. By fostering strong partnerships with well-established plastic tooling manufacturers, companies can navigate the intricacies of production, adapt to changing market conditions, and ultimately thrive in a competitive landscape.
To learn more about how to optimize your production with plastic tooling, visit deepmould.net and explore our comprehensive services designed to meet your manufacturing needs.