Exploring Vacuum Casting: The Revolution in Product Design and 3D Printing
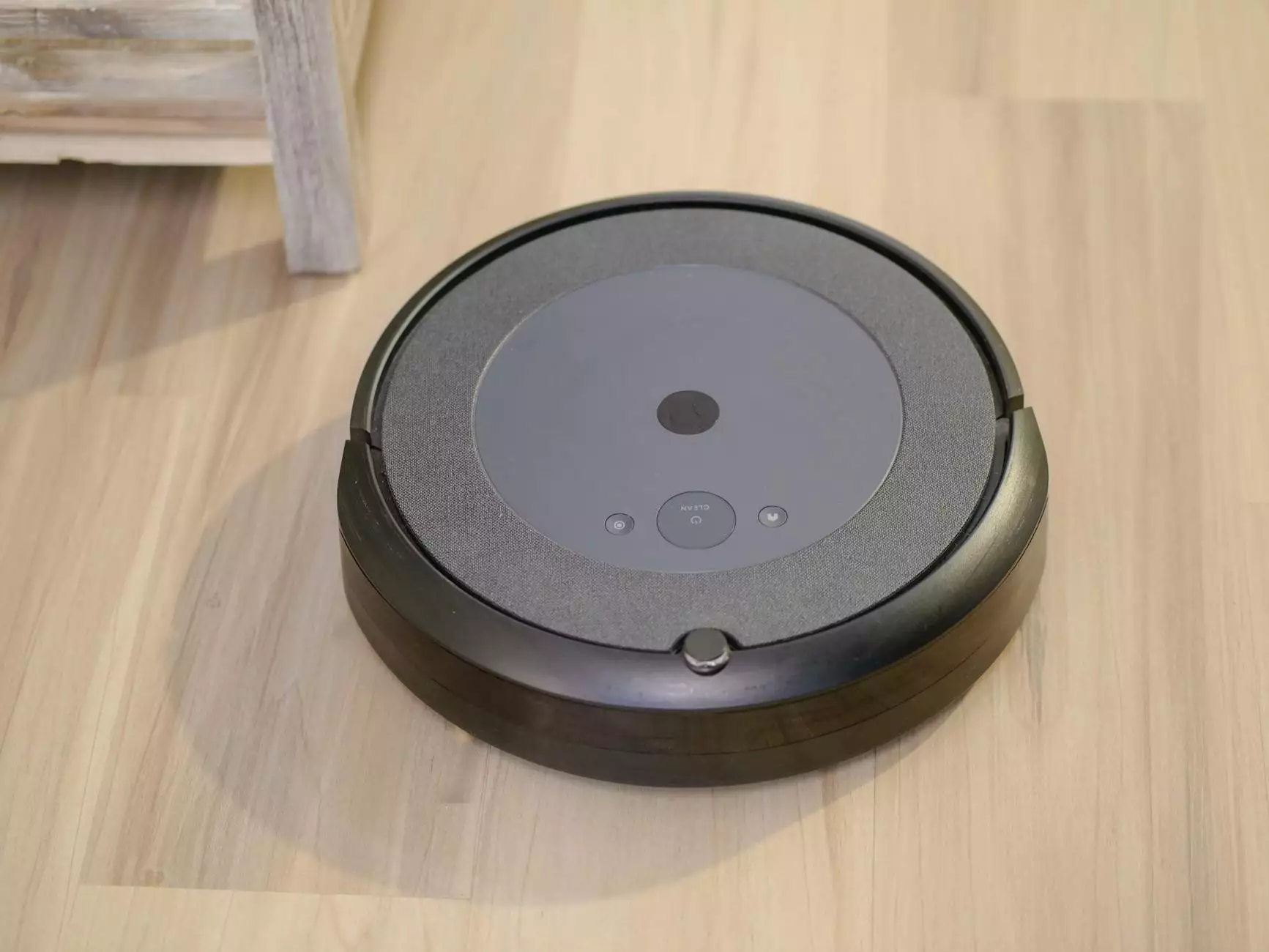
Vacuum casting has emerged as a groundbreaking technique in the field of product design and manufacturing, particularly in the realms of art supplies and 3D printing. This innovative method not only streamlines the production process but also enhances the quality and precision of manufactured parts. As businesses like arti90.com leverage this technology, understanding its advantages and applications becomes crucial for industry professionals and enthusiasts alike.
Understanding Vacuum Casting
Vacuum casting is a versatile manufacturing process primarily used for creating high-precision prototypes and small batches of products. By combining a silicone mold with vacuum pressure, manufacturers can produce intricate designs with remarkable accuracy. This technique is particularly suited for materials like polyurethane, which can mimic the properties of various plastics and metals.
How Vacuum Casting Works
The vacuum casting process consists of several key steps:
- Creation of a Master Model: The first step involves crafting a master model, typically through 3D printing or machining. This model represents the final product's design.
- Mold Preparation: A silicone mold is created around the master model. The flexibility of silicone allows for intricate designs and undercuts.
- Pouring the Material: Once the mold is cured, the selected casting material (often polyurethane) is poured into the mold.
- Applying Vacuum Pressure: The mold is placed in a vacuum chamber, where air is extracted. This process reduces air bubbles within the material, enhancing the final product's clarity and strength.
- Curing and Demolding: After the material cures, the final casting is removed from the silicone mold, ready for finishing touches.
The Benefits of Vacuum Casting
Vacuum casting offers numerous advantages for businesses involved in art supplies, product design, and 3D printing. Here are some of the most significant benefits:
- Cost-Effective Prototyping: Creating a silicone mold is relatively inexpensive compared to traditional techniques, which often require costly tooling and equipment.
- High-Quality Finish: The use of vacuum pressure eliminates air bubbles, resulting in smooth surfaces and detailed designs.
- Flexible Material Options: Manufacturers can choose from a variety of resins that can replicate different textures, colors, and mechanical properties.
- Fast Turnaround Time: Unlike injection molding, which can take weeks for tooling, vacuum casting allows for rapid prototyping, often within days.
- Low Volume Production: Ideal for small batches, vacuum casting is perfect for startups and businesses that need limited runs of quality prototypes.
Applications of Vacuum Casting
With its versatility, vacuum casting finds applications across various industries:
1. Product Design and Prototyping
Designers utilize vacuum casting to create realistic models for testing functionality and aesthetics. This method allows for quick adjustments to designs before mass production.
2. Art Supplies
In the realm of art supplies, vacuum casting enables artists and manufacturers to produce unique tools ranging from custom brush handles to intricate sculpting tools. By leveraging this technique, artisans can accurately reproduce their designs without sacrificing fidelity.
3. 3D Printing Complement
While 3D printing excels at rapid prototyping, vacuum casting enhances the durability and finish of printed models. Combining the two methods yields high-quality prototypes suitable for functional testing.
4. Engineering and Manufacturing
Engineers favor vacuum casting for producing components that require precise dimensions and materials that simulate production-grade parts, thus saving time and reducing waste during the testing phase.
Challenges and Considerations in Vacuum Casting
Despite its numerous advantages, vacuum casting is not without challenges. Here are some limitations to consider:
- Material Restrictions: While many resins can be used, not all materials are suitable for vacuum casting, which may limit options for certain applications.
- Durability of Molds: Silicone molds have a finite lifespan, and repeated use may lead to degradation, affecting the quality of subsequent castings.
- Skill Requirement: Effective vacuum casting requires skilled technicians capable of producing quality master models and molding processes.
Future Trends in Vacuum Casting and Product Design
The future of vacuum casting looks bright, driven by advancements in technology and material science. Here are some emerging trends to watch:
1. Integration with Additive Manufacturing
As 3D printing technology evolves, we can expect to see enhanced integration with vacuum casting methods, resulting in stronger, lighter, and more complex designs.
2. Sustainable Materials
With the increasing importance of sustainability, manufacturers are actively researching biocompatible and eco-friendly casting materials for use in vacuum casting.
3. Automated Casting Processes
As automation continues to permeate manufacturing, automated vacuum casting processes may become more prevalent, improving efficiency and consistency across productions.
Conclusion
In conclusion, vacuum casting is a powerful tool that revolutionizes the fields of product design, art supplies, and 3D printing. Its benefits, such as cost-effectiveness, high-quality finishes, and flexibility, make it an attractive choice for manufacturers and designers alike. As technology continues to advance, those who embrace vacuum casting will undoubtedly lead the way in innovation and design excellence.
For businesses interested in harnessing the power of vacuum casting, partnering with experienced providers and leveraging resources like arti90.com can help facilitate the process and ensure successful outcomes.
Ready to Dive Deeper?
If you're looking to explore more about vacuum casting or its applications in art supplies and product design, consider reaching out to professionals in the industry. Engaging with experts can provide insights into best practices and potential partnerships to elevate your projects.