Mastering Plastic Molding Tools: A Comprehensive Guide for Metal Fabricators
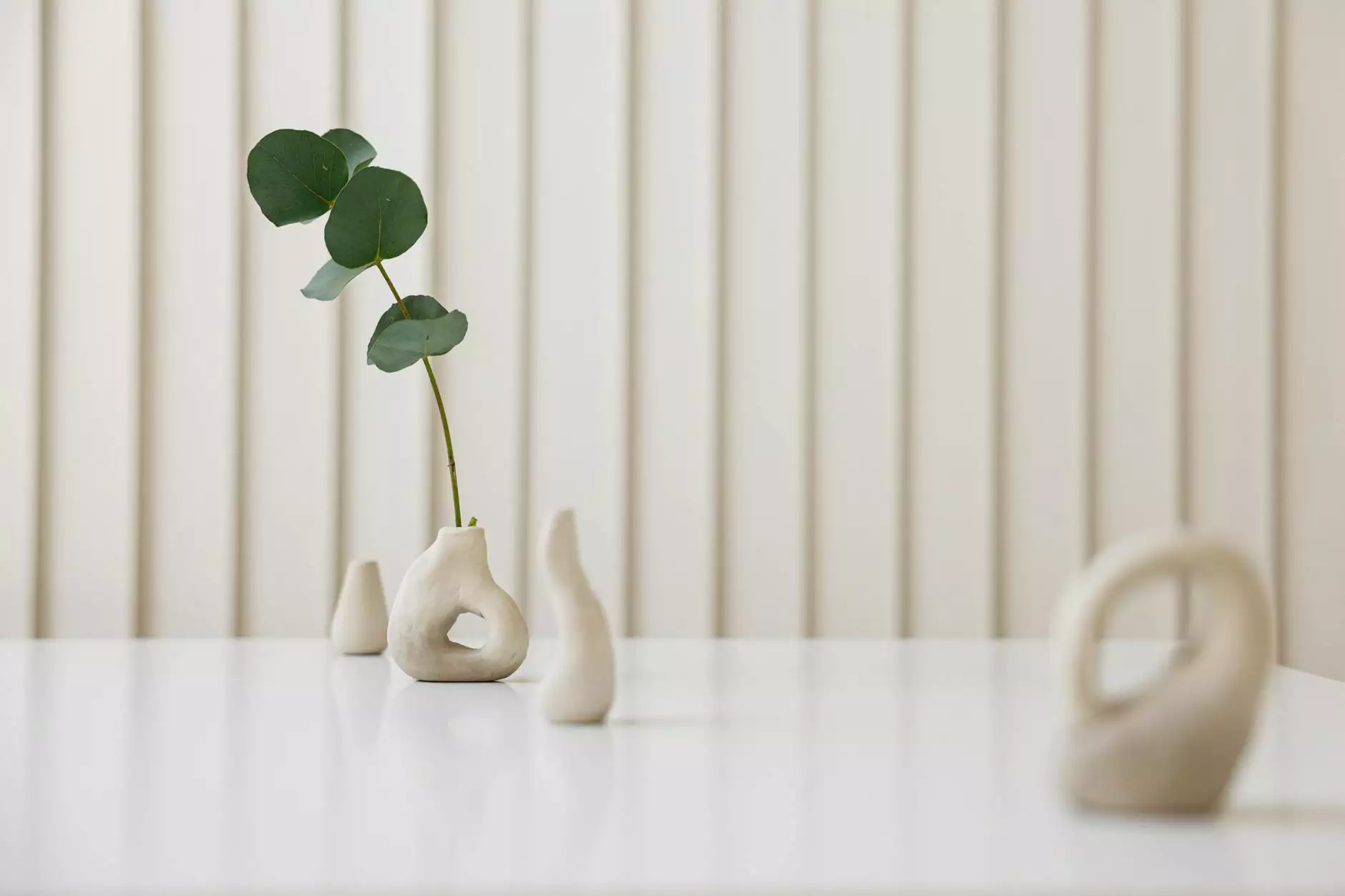
In the world of metal fabrication, the use of advanced manufacturing techniques has become increasingly vital in staying competitive. Among these techniques, the utilization of plastic molding tools has emerged as a significant game changer. Whether you are a seasoned professional or new to the field, understanding the role and advantages of plastic molding tools is crucial. In this article, we will explore the intricacies of plastic molding tools, their applications, and how they revolutionize the metal fabrication industry.
What Are Plastic Molding Tools?
Plastic molding tools are specifically designed equipment used in the production of plastic products through various molding processes. These tools allow for precise shaping and formation of materials, enabling manufacturers to create intricate designs and specifications. Common types of plastic molding include:
- Injection Molding: This process involves injecting molten plastic into a mold to create the desired shape.
- Blow Molding: Used primarily for hollow objects, this technique inflates a hot plastic tube within a mold.
- Extrusion Molding: This method forms long objects like pipes or sheets by forcing material through a shaped die.
- Rotational Molding: Suitable for producing large, hollow parts, this technique rotates a mold on multiple axes.
Why Are Plastic Molding Tools Important for Metal Fabricators?
The integration of plastic molding tools into the metal fabrication process offers several advantages:
- Cost Efficiency: Utilizing plastic components can significantly reduce production costs by minimizing material waste and decreasing processing times.
- Design Flexibility: Plastic molding allows for complex shapes and designs that might be challenging or costly to achieve with traditional metalworking techniques.
- Weight Reduction: Plastic parts are often lighter than metal counterparts, which can improve the overall performance and efficiency of the final product.
- Durability: Modern plastics provide remarkable resistance to corrosion, moisture, and various chemicals, ensuring longevity in demanding environments.
- Innovation: The continual evolution of plastic materials and molding techniques can lead to innovative products that fulfill specific market needs.
Key Features of Modern Plastic Molding Tools
For metal fabricators, selecting the right plastic molding tools is paramount for optimal production efficiency and quality. Here are vital features to consider:
Precision Engineering
Precision in molding tools ensures that every product meets the required specifications. High-quality molds are manufactured using advanced machining techniques, resulting in exact replicas of the intended designs.
Material Quality
The durability and performance of a molding tool depend significantly on the materials used in its fabrication. High-grade steel or aluminum is preferred to withstand the repetitive cycles of molding processes while maintaining structural integrity.
Ease of Maintenance
Maintenance-friendly plastic molding tools can save time and costs associated with downtime. Tools designed for easy disassembly and cleaning enable quicker turnaround between different production runs.
Compatibility with Advanced Technologies
Incorporating advanced technologies like CAD/CAM systems into the design and fabrication of molding tools can enhance efficiency and precision. These technologies allow for rapid prototyping and testing of design modifications.
Applications of Plastic Molding Tools in Metal Fabrication
The versatility of plastic molding tools in metal fabrication spans across industries. Some key applications include:
Automotive Industry
In the automotive sector, plastic components molded from plastic tools are becoming increasingly common. They are utilized in various parts, including dashboards, bumpers, and electrical housings, reducing overall vehicle weight and improving fuel efficiency.
Consumer Electronics
Plastic molds play an essential role in the production of consumer electronics. Many devices utilize molded plastic components for structural and aesthetic purposes, making the manufacturing process more efficient.
Medical Devices
The medical industry relies on precise plastic components for devices such as syringes, IV bags, and surgical instruments. Advanced plastic molding tools ensure that these products meet stringent regulatory standards while optimizing production processes.
Packaging
Plastic molding tools are also instrumental in developing packaging solutions that are lightweight yet durable. From bottles to containers, molded plastics offer effective protection and ease of transportation, contributing to sustainability efforts.
How to Choose the Right Plastic Molding Tools?
Selecting the appropriate plastic molding tools for your specific needs requires careful consideration. Here are several factors to keep in mind:
Project Requirements
Assess the specifications and scale of your project. Different molding processes may suit particular projects better than others, so understanding your production volume and product design is essential.
Manufacturer Reputation
Choose a reliable manufacturer with a proven track record in producing high-quality molding tools. Research their industry experience and customer reviews to ensure you are making a sound investment.
Cost Considerations
While budget constraints are crucial, opting for the cheapest solution may lead to subpar quality. Evaluate the long-term costs of maintenance, repairs, and efficiency before making a decision.
Technical Support and Training
Many manufacturers offer support and training for their molding tools. Choose a supplier that provides comprehensive assistance, ensuring your team is well-equipped to operate and maintain the tools effectively.
Future Trends in Plastic Molding Technologies
The landscape of plastic molding tools is continuously evolving. Here are some trends to watch for in the near future:
Sustainability Focus
With increasing environmental concerns, there is a growing trend towards developing biodegradable plastics and utilizing recycled materials in the molding process. Manufacturers are exploring eco-friendly alternatives that reduce carbon footprints.
Integration of Automation
The rise of automation in manufacturing processes is changing how plastic molding is performed. Automated systems can enhance precision, speed, and efficiency, reducing human error and labor costs.
3D Printing Innovations
3D printing is becoming more prevalent for creating molds and components. This innovation enables rapid prototyping, design flexibility, and cost-effective short-run production, catering to the needs of various industries.
Conclusion: Embracing the Future of Metal Fabrication with Plastic Molding Tools
The incorporation of plastic molding tools into the metal fabrication industry signifies a crucial step towards modernization and efficiency. As the landscape of manufacturing continues to evolve, fabricators who embrace these technologies will enhance their product offerings and maintain a competitive edge.
By understanding the capabilities of plastic molding tools, metal fabricators can expand their service offerings, reduce costs, and drive innovation. As we move forward, keeping abreast of market trends and technological advancements will be essential for success.
For further information on plastic molding tools and their applications in metal fabrication, visit Deep Mould.