Understanding Lathe Parts Factories: The Backbone of Metal Fabrication
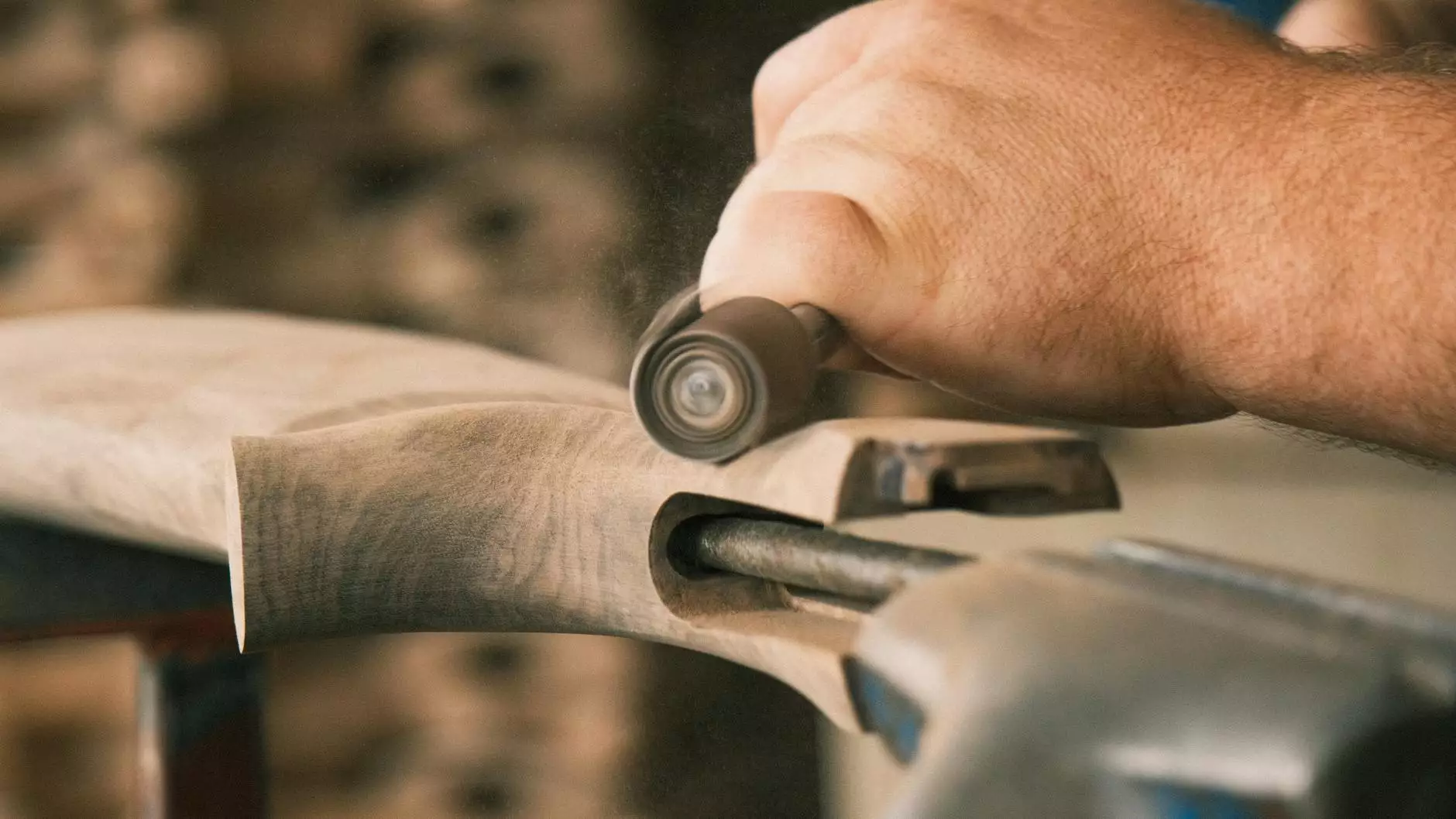
The world of metal fabrication is intricate, multifaceted, and essential for numerous industries. Among its critical components lies the operation of a lathe parts factory. This guide aims to delve into the various aspects of lathe parts manufacturing, exploring how it enhances production capabilities and the overall efficiency of businesses in the sector.
What is a Lathe Parts Factory?
A lathe parts factory specializes in producing precision parts using lathe machines, which are essential for shaping and cutting materials like metal, wood, and plastic. The significance of the lathe in manufacturing cannot be overstated, as it allows for:
- Modularity: Parts can be created with exact specifications.
- Repetition: Ensures uniformity in the production line.
- Flexibility: Capable of working with various materials and designs.
The Importance of Lathe Parts in Metal Fabrication
Lathe parts are crucial components used in a wide array of applications, hence the necessity for high-quality production in a lathe parts factory. The benefits include:
- Precision Engineering: Lathe parts are machined to meet exacting standards, which is vital for applications in aerospace, automotive, and manufacturing industries.
- Cost Efficiency: By automating the production of lathe parts, factories reduce labor costs and minimize waste.
- Speed: Automated lathe machining allows companies to fulfill orders rapidly, meeting market demands without compromise.
Processes Involved in Lathe Parts Manufacturing
The manufacturing of lathe parts involves several critical processes that ensure precision and quality throughout production. Here are some key steps:
1. Design Engineering
The first step in the bespoke manufacturing of lathe parts is design engineering. Engineers utilize Computer-Aided Design (CAD) software to create detailed schematics of parts. This stage involves collaboration with clients to ensure that the parts meet specific requirements and industry standards.
2. Material Selection
The choice of material is paramount in lathe parts production. Common materials include:
- Steel
- Aluminum
- Copper
- Plastic composites
Each material has distinct properties that can influence the durability and effectiveness of the final product.
3. Machining Processes
Once designs are finalized and materials selected, the following machining processes are employed:
- Turning: This is the fundamental process where the lathe rotates the workpiece against a stationary cutting tool.
- Milling: Involves the cutting of materials through rotating multi-point tools.
- Drilling: Creates holes in materials for screws and fasteners.
- Grinding: Finishes surfaces to the required specifications.
4. Quality Control
Quality control is an integral part of the operations of a lathe parts factory. After machining, parts undergo rigorous testing to ensure they meet predefined standards. This can include:
- Dimensional Inspection: Verifying the measurements of parts against specifications.
- Material Testing: Ensuring the materials used meet the necessary strength and durability requirements.
- Functional Testing: Assessing the parts' performance in real-world applications.
Innovations in Lathe Parts Manufacturing
The advancement of technology has brought significant innovations to lathe parts manufacturing. Some noteworthy trends include:
- Automation: The integration of robotics and automated systems has enhanced efficiency in production lines.
- 3D Printing: Companies are increasingly utilizing additive manufacturing to optimize part designs before full production.
- IoT and Smart Factories: The use of Internet of Things (IoT) in machinery allows for real-time monitoring and maintenance, improving production efficiency.
How a Lathe Parts Factory Can Benefit Your Business
Partnering with a reputable lathe parts factory offers numerous advantages that can transform your production capabilities:
1. Enhanced Quality and Reliability
Working with experienced fabricators ensures that the lathe parts produced are of the highest quality. This reliability can lead to improved product performance and customer satisfaction.
2. Scalability
Whether you require small batches or large-scale production runs, a lathe parts factory can scale operations to meet fluctuating demands while maintaining quality standards.
3. Access to Expertise
Collaboration with a specialist lathe parts factory grants access to a wealth of experience and knowledge in metal fabrication, enabling businesses to troubleshoot and innovate effectively.
Selecting the Right Lathe Parts Factory
When choosing a lathe parts factory, consider the following criteria to ensure optimal results:
- Experience and Reputation: Look for factories with a solid track record and positive client testimonials in the industry.
- Technological Capabilities: A modern factory equipped with advanced machinery and technology will offer better quality and faster turnaround times.
- Certifications: Ensure the factory complies with industry standards and has the necessary certifications, such as ISO.
Future of Lathe Parts Factories
As industries evolve, so too will the operations of lathe parts factories. The future seems bright, with ongoing innovations expected to dominate production. This includes adapting to sustainable practices, embracing green manufacturing methods, and focusing on energy-efficient technologies that reduce the carbon footprint.
Conclusion
In conclusion, the role of a lathe parts factory is integral to the metal fabrication industry. The precision, efficiency, and quality assurance that such factories provide cannot be overlooked. As businesses continue to seek ways to enhance manufacturing processes, understanding and investing in high-quality lathe parts becomes increasingly crucial. By leveraging the advanced capabilities of a professional lathe parts factory, companies can stay competitive and ensure they meet the evolving demands of their industries.